Med utviklingen av moderne vitenskap og teknologi brukes flere og flere ingeniørmaterialer med høy hardhet, mens den tradisjonelle dreieteknologien ikke er kompetent eller ikke kan oppnå bearbeiding av noen materialer med høy hardhet i det hele tatt.Belagt karbid, keramikk, PCBN og andre superharde verktøymaterialer har høy hardhet ved høy temperatur, slitestyrke og termokjemisk stabilitet, som gir den mest grunnleggende forutsetningen for skjæring av materialer med høy hardhet, og har oppnådd betydelige fordeler i produksjonen.Materialet som brukes av det superharde verktøyet og dets verktøystruktur og geometriske parametere er de grunnleggende elementene for å realisere hard dreiing.Derfor er det avgjørende hvordan man velger det superharde verktøymaterialet og designer en fornuftig verktøystruktur og geometriske parametere for å oppnå stabil harddreiing!
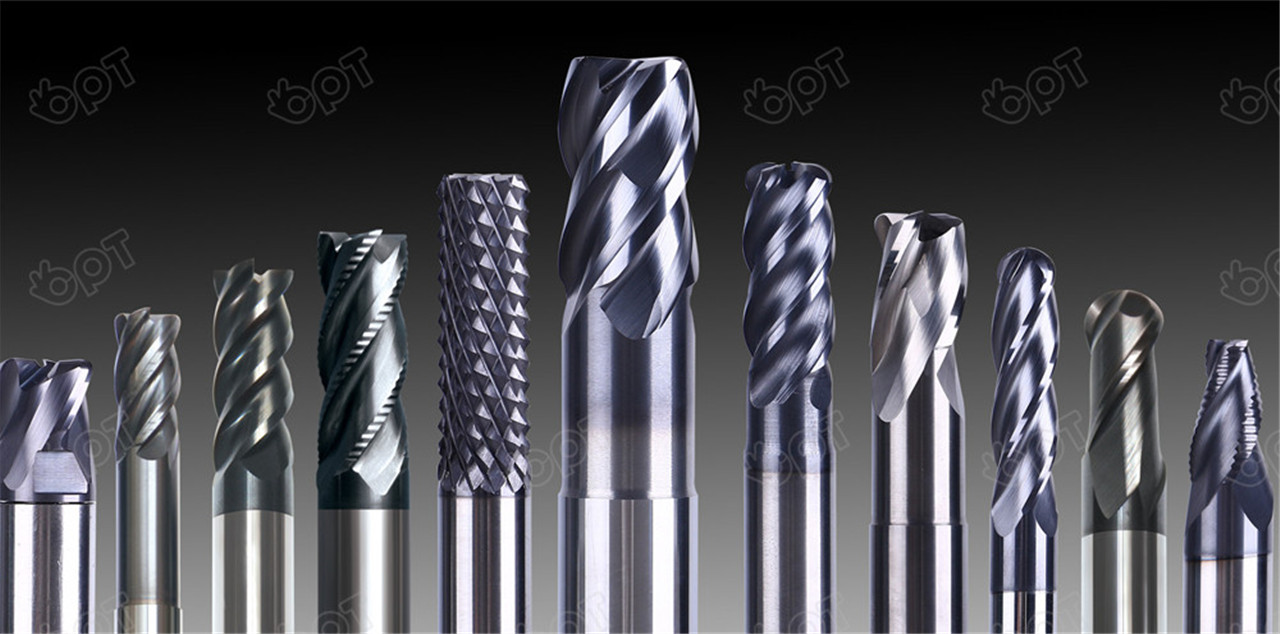
(1) Belagt hardmetall
Påfør ett eller flere lag med TiN, TiCN, TiAlN og Al3O2 med god slitestyrke på hardmetallverktøy med god seighet, og tykkelsen på belegget er 2-18 μm.Belegget har vanligvis en mye lavere varmeledningsevne enn verktøysubstratet og arbeidsstykkematerialet, noe som svekker den termiske effekten til verktøysubstratet;På den annen side kan det effektivt forbedre friksjonen og adhesjonen i skjæreprosessen og redusere genereringen av skjærevarme.
Selv om PVD-belegg viser mange fordeler, har noen belegg som Al2O3 og diamant en tendens til å ta i bruk CVD-beleggsteknologi.Al2O3 er et slags belegg med sterk varmebestandighet og oksidasjonsmotstand, som kan skille varmen som genereres ved kutting fra det spesifikke verktøyet.CVD-beleggsteknologi kan også integrere fordelene med ulike belegg for å oppnå den beste kutteeffekten og møte behovene til kutting.
Sammenlignet med hardmetallverktøy har belagte hardmetallverktøy forbedret styrke, hardhet og slitestyrke.Når du dreier arbeidsstykket med en hardhet på HRC45~55, kan lavkostbelagt hardmetall realisere høyhastighetsdreiing.De siste årene har noen produsenter forbedret ytelsen til belagte verktøy ved å forbedre beleggsmaterialer og andre metoder.For eksempel bruker noen produsenter i USA og Japan sveitsisk AlTiN-beleggsmateriale og ny beleggspatentert teknologi for å produsere belagte blader med hardhet så høy som HV4500~4900, som kan kutte HRC47~58 formstål med en hastighet på 498,56m/min. .Når dreietemperaturen er opp til 1500 ~ 1600 ° C, reduseres ikke hardheten og oksiderer ikke.Bladets levetid er fire ganger så lang som for det generelle belagte bladet, mens kostnaden bare er 30 %, og vedheften er god.
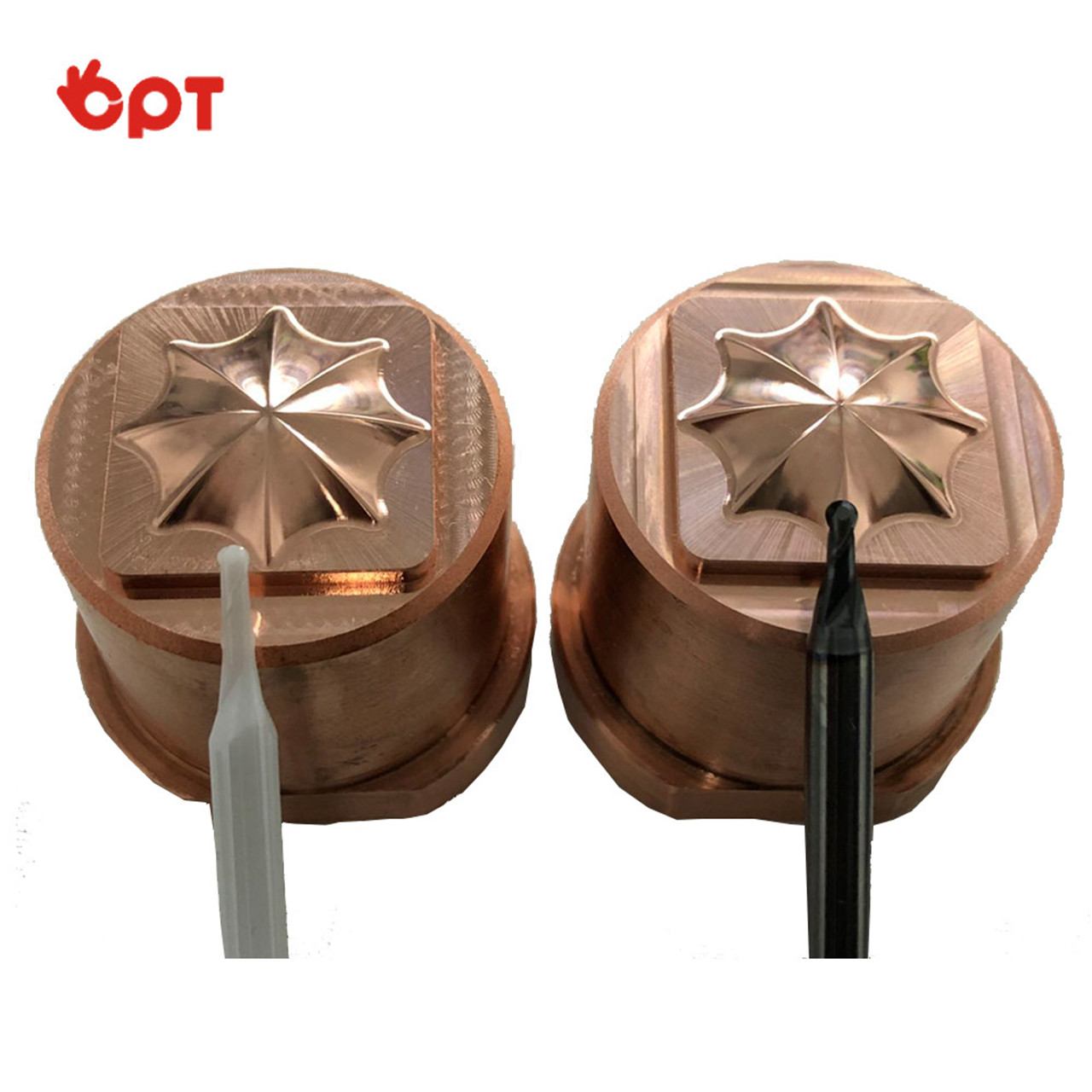
(2) Keramisk materiale
Med kontinuerlig forbedring av sammensetningen, strukturen og presseprosessen, spesielt utviklingen av nanoteknologi, gjør keramiske verktøymaterialer det mulig å herde keramiske verktøy.I nær fremtid kan keramikk forårsake den tredje revolusjonen innen skjæring etter høyhastighetsstål og hardmetall.Keramiske verktøy har fordelene med høy hardhet (HRA91~95), høy styrke (bøyestyrke 750~1000MPa), god slitestyrke, god kjemisk stabilitet, god vedheftsmotstand, lav friksjonskoeffisient og lav pris.Ikke bare det, keramiske verktøy har også høy hardhet ved høy temperatur, som når HRA80 ved 1200 ° C.
Under normal skjæring har det keramiske verktøyet en meget høy holdbarhet, og skjærehastigheten kan være 2 ~ 5 ganger høyere enn for sementert karbid.Den er spesielt egnet for maskinering av materialer med høy hardhet, etterbehandling og høyhastighets maskinering.Den kan kutte ulike herdet stål og herdet støpejern med hardhet opp til HRC65.Vanligvis brukt er aluminabasert keramikk, silisiumnitridbasert keramikk, cermets og whisker-herdet keramikk.
Alumina-baserte keramiske verktøy har høyere rød hardhet enn sementert karbid.Generelt vil skjærekanten ikke produsere plastisk deformasjon under høyhastighets skjæreforhold, men dens styrke og seighet er svært lav.For å forbedre dens seighet og slagfasthet, kan ZrO eller TiC og TiN-blanding tilsettes.En annen metode er å legge til rent metall eller silisiumkarbid værhår.I tillegg til høy rød hardhet, har silisiumnitridbasert keramikk også god seighet.Sammenlignet med aluminabasert keramikk, er dens ulempe at det er lett å produsere høytemperaturdiffusjon ved maskinering av stål, noe som forverrer verktøyslitasje.Silisiumnitridbasert keramikk brukes hovedsakelig til intermitterende dreiing og fresing av grått støpejern.
Cermet er et slags karbidbasert materiale, der TiC er den viktigste harde fasen (0,5-2 μm) De er kombinert med Co eller Ti bindemidler og ligner på hardmetallverktøy, men de har lav affinitet, god friksjon og god Slitestyrke.Den tåler høyere skjæretemperatur enn konvensjonell hardmetall, men den mangler slagfastheten til hardmetall, seigheten ved tung kutting og styrken ved lav hastighet og stor mating.
(3) Kubisk bornitrid (CBN)
CBN er nest etter diamant i hardhet og slitestyrke, og har utmerket høytemperaturhardhet.Sammenlignet med keramikk er dens varmebestandighet og kjemiske stabilitet litt dårlig, men slagstyrken og anti-knusningsytelsen er bedre.Den er allment anvendelig for skjæring av herdet stål (HRC ≥ 50), perlitisk grått støpejern, kjølt støpejern og superlegering.Sammenlignet med hardmetallverktøy kan skjærehastigheten økes med én størrelsesorden.
Det sammensatte polykrystallinske kubisk bornitrid (PCBN) verktøyet med høyt CBN-innhold har høy hardhet, god slitestyrke, høy trykkfasthet og god slagfasthet.Dens ulemper er dårlig termisk stabilitet og lav kjemisk inerthet.Den er egnet for kutting av varmebestandige legeringer, støpejern og jernbaserte sintrede metaller.Innholdet av CBN-partikler i PCBN-verktøy er lavt, og hardheten til PCBN-verktøy som bruker keramikk som bindemiddel er lav, men det veier opp for den dårlige termiske stabiliteten og lave kjemiske tregheten til det førstnevnte materialet, og er egnet for skjæring av herdet stål.
Ved skjæring av grått støpejern og herdet stål kan keramisk verktøy eller CBN-verktøy velges.Av denne grunn bør kostnad-nytte og prosesskvalitetsanalyse utføres for å bestemme hvilken du skal velge.Når skjærehardheten er lavere enn HRC60 og liten matehastighet er vedtatt, er keramisk verktøy et bedre valg.PCBN-verktøy er egnet for å kutte arbeidsstykker med hardhet høyere enn HRC60, spesielt for automatisk maskinering og høypresisjonsmaskinering.I tillegg er restspenningen på arbeidsstykkets overflate etter kutting med PCBN-verktøy også relativt stabil enn den med keramiske verktøy under samme flankeslitasje.
Når du bruker PCBN-verktøy for å tørkeskjære herdet stål, bør følgende prinsipper også følges: velg en stor skjæredybde så langt som mulig under forutsetning av at maskinverktøyets stivhet tillater det, slik at varmen som genereres i skjæreområdet kan myke opp metallet foran på kanten lokalt, noe som effektivt kan redusere slitasjen på PCBN-verktøyet.I tillegg, når du bruker en liten skjæredybde, bør det også tas i betraktning at den dårlige varmeledningsevnen til PCBN-verktøyet kan gjøre at varmen i skjæreområdet diffunderer for sent, og skjærområdet kan også gi åpenbar metallmykningseffekt. slitasje av skjærekant.
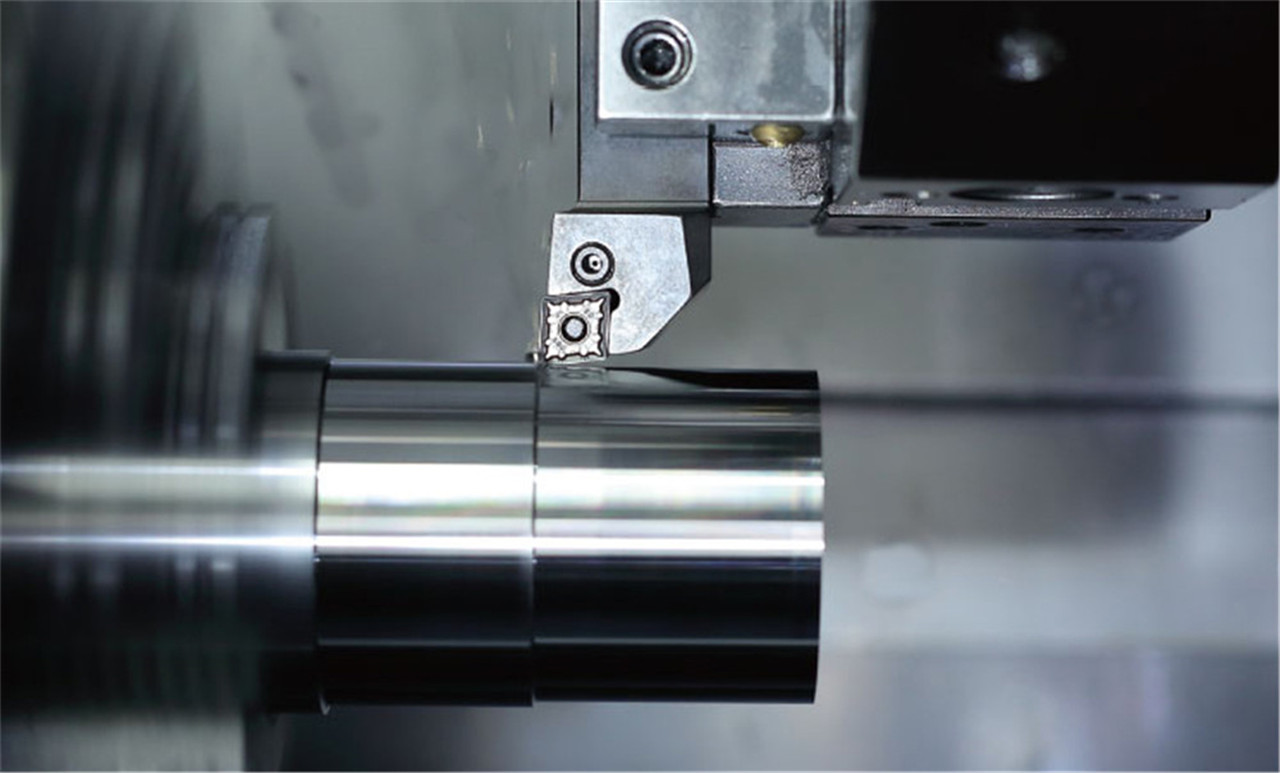
2. Bladstruktur og geometriske parametere for superharde verktøy
Den rimelige bestemmelsen av verktøyets form og geometriske parametere er svært viktig for å gi full spillerom til verktøyets kutteytelse.Når det gjelder verktøystyrke, er verktøytuppstyrken til forskjellige bladformer fra høy til lav: rund, 100 ° diamant, firkantet, 80 ° diamant, trekant, 55 ° diamant, 35 ° diamant.Etter at bladmaterialet er valgt, skal bladformen med høyest styrke velges.Harde snublader bør også velges så store som mulig, og grovbearbeiding bør gjøres med runde og store spissbueradiusblader.Spissbueradius er ca. 0,8 ved etterbehandling μ Ca m.
De herdede stålsponene er røde og myke bånd, med stor sprøhet, lett å bryte og ikke bindende.Den herdede stålskjæreoverflaten er av høy kvalitet og produserer generelt ikke sponakkumulering, men skjærekraften er stor, spesielt den radielle skjærekraften er større enn hovedskjærekraften.Derfor bør verktøyet bruke en negativ frontvinkel (gå ≥ - 5 °) og en stor ryggvinkel (ao=10°~15°).Hovedavbøyningsvinkelen avhenger av stivheten til maskinverktøyet, vanligvis 45 ° ~ 60 °, for å redusere skravling av arbeidsstykket og verktøyet.
Innleggstid: 24. februar 2023